When it comes to constructing curved concrete forms, plywood has emerged as an innovative and versatile material. By understanding the properties of plywood and the benefits it offers, construction professionals can take advantage of its cost-effectiveness, durability, and strength. However, like any construction technique, using plywood for curved concrete forms also presents unique challenges that need to be addressed. In this article, we will explore the basics of plywood, its application in concrete forms, and delve into the advantages and challenges it brings. Additionally, we will discuss the future trends in plywood use for curved concrete forms, including technological advancements and sustainability considerations.
Understanding Plywood and Concrete Forms
Plywood offers several advantages when it comes to constructing plywood curved concrete forms. Firstly, its flexibility allows it to bend and conform to the desired shape, making it an ideal material for creating complex curves. Furthermore, plywood’s strength and stability ensure that the formwork remains intact during the concrete pouring process, preventing any structural failures.
The Basics of Plywood
Plywood is a type of engineered wood made from thin layers of wood veneer glued together with adjacent layers having their grain rotated 90 degrees to one another. This cross-grain construction gives plywood its characteristic strength and stability. Plywood comes in various grades and thicknesses, allowing for flexibility in its application.
One of the key advantages of plywood is its versatility. It is commonly used in construction for structural applications such as flooring, roofing, walls, and formwork. Plywood’s uniform strength and resistance to warping make it an ideal choice for projects that require durability and reliability. Additionally, plywood is cost-effective compared to solid wood, making it a popular choice among builders and contractors.
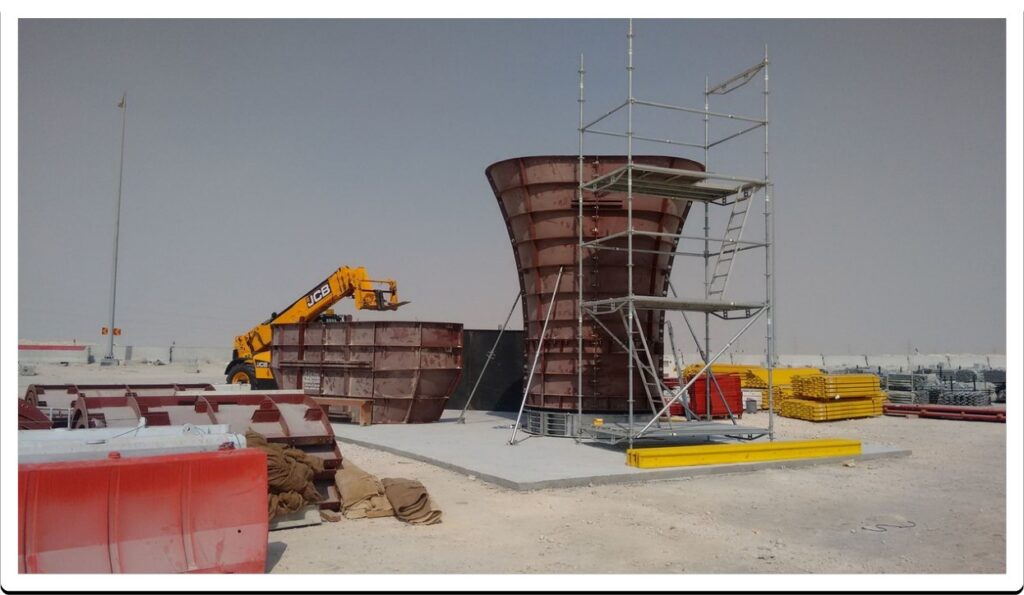
What are Concrete Forms?
Concrete forms are temporary structures used to shape and support freshly poured concrete until it sets and gains sufficient strength. They come in different types, including flat forms, column forms, and curved forms. Curved concrete forms are essential for creating unique architectural designs, such as curved walls, facades, and various decorative elements.
Flat forms are commonly used for horizontal surfaces like slabs and pavements, providing a smooth and level finish. Column forms are used to create vertical concrete elements such as pillars and posts. These forms are designed to withstand the pressure exerted by the wet concrete and ensure that the final structure retains its intended shape and dimensions. In contrast, curved forms offer architects and designers the freedom to explore innovative shapes and contours, adding aesthetic appeal to concrete structures.
The Innovation in Using Plywood for Curved Concrete Forms
Why Plywood for Curved Concrete Forms?
Moreover, plywood is a cost-effective option compared to other materials used for forming curved concrete. Its availability and affordability make it a popular choice among builders and contractors looking to achieve unique and intricate designs without breaking the bank. Additionally, plywood can be easily sourced from local suppliers, reducing lead times and ensuring timely project completion.
The Process of Using Plywood in Forming Curved Concrete
The process of using plywood for forming curved concrete involves several steps. First, the desired curve is determined and a template is created. This template is then used as a guide to cut the plywood into curved segments which are assembled and fastened together to form the complete formwork. Once the formwork is in place, reinforcing bars can be added, and concrete can be poured into the formwork, taking the shape of the curve. After the concrete has set, the formwork is stripped, revealing the beautifully curved concrete element.
Furthermore, plywood formwork can be reused multiple times, making it a sustainable choice for construction projects. This reusability not only reduces waste but also minimizes the environmental impact of the construction process. By incorporating plywood formwork into curved concrete designs, builders can achieve both aesthetic appeal and sustainability, creating structures that are not only visually striking but also environmentally conscious.
Advantages of Using Plywood for Curved Concrete Forms
Cost-Effectiveness of Plywood
One of the major advantages of using plywood for curved concrete forms is its cost-effectiveness. Plywood is relatively inexpensive compared to other materials commonly used for curved formwork, such as specialized curved metal panels. This cost savings can make a significant difference in construction budgets, especially when there is a need for multiple curved elements.
Furthermore, plywood is readily available in various thicknesses and sizes, making it a versatile option for different project requirements. Its affordability and accessibility make plywood a practical choice for contractors looking to optimize their resources without compromising on quality. Learn more about affordability on https://library.educause.edu/topics/leadership-and-management/affordability
Durability and Strength of Plywood Forms
Plywood forms are highly durable and can withstand the rigors of the concrete pouring process. The cross-grain construction of plywood enhances its strength, allowing it to handle the pressure exerted by the wet concrete without flexing or deforming. Moreover, plywood forms can be reused multiple times, further contributing to their cost-effectiveness and sustainability.
In addition to their strength, plywood forms offer a smooth surface finish to the cured concrete, reducing the need for extensive finishing work. This smooth finish not only enhances the aesthetic appeal of the concrete elements but also improves their overall durability by minimizing surface imperfections that could lead to moisture penetration or structural weaknesses.
Challenges and Solutions in Using Plywood for Curved Concrete Forms
Common Difficulties in Using Plywood
While plywood brings numerous benefits to curved concrete formwork, it also presents some challenges. One common difficulty is achieving a smooth surface finish on curved forms. Plywood’s natural texture can transfer to the concrete, resulting in imperfections on the final surface. Additionally, plywood is prone to swelling and warping when exposed to moisture, which can affect the integrity of the formwork.
Another challenge faced when using plywood for curved concrete forms is the risk of delamination. Delamination occurs when the layers of plywood separate, compromising the strength and durability of the formwork. This can lead to structural issues and a decrease in the quality of the concrete finish. Proper handling and storage of plywood sheets are crucial in preventing delamination.
Overcoming Challenges in Plywood Use
To overcome the challenges associated with using plywood in curved concrete forms, several measures can be taken. Applying a release agent or form-facing material can help achieve a smoother finish on the concrete surface. Treating the plywood with sealants or coatings can also enhance its resistance to moisture, preventing swelling and warping. By using proper formwork release systems and regular maintenance, the lifespan of the plywood forms can be extended.
Furthermore, incorporating additional bracing and support systems can help prevent warping and maintain the desired shape of the curved formwork. By ensuring that the plywood is securely fastened and supported throughout the concrete pouring process, the risk of deformation or misalignment is minimized. Attention to detail in the construction and reinforcement of the formwork is essential for achieving high-quality curved concrete structures.
Future Trends in Plywood and Curved Concrete Forms
Technological Advancements in Plywood Use
The future of plywood and curved concrete forms is driven by technological advancements. Computer-aided design (CAD) and computer-aided manufacturing (CAM) technologies are now being used to precisely cut curved plywood segments, improving the efficiency and accuracy of the formwork assembly process. This level of precision allows for the creation of complex and intricate curved designs that were previously difficult to achieve.
Furthermore, the development of advanced coatings and treatments can further enhance the durability and moisture resistance of plywood, ensuring its longevity in curved formwork applications. These coatings not only protect the plywood from moisture damage but also provide a smooth surface finish, reducing the need for additional surface treatments and saving both time and money during the construction process. To learn more about moisture click here.
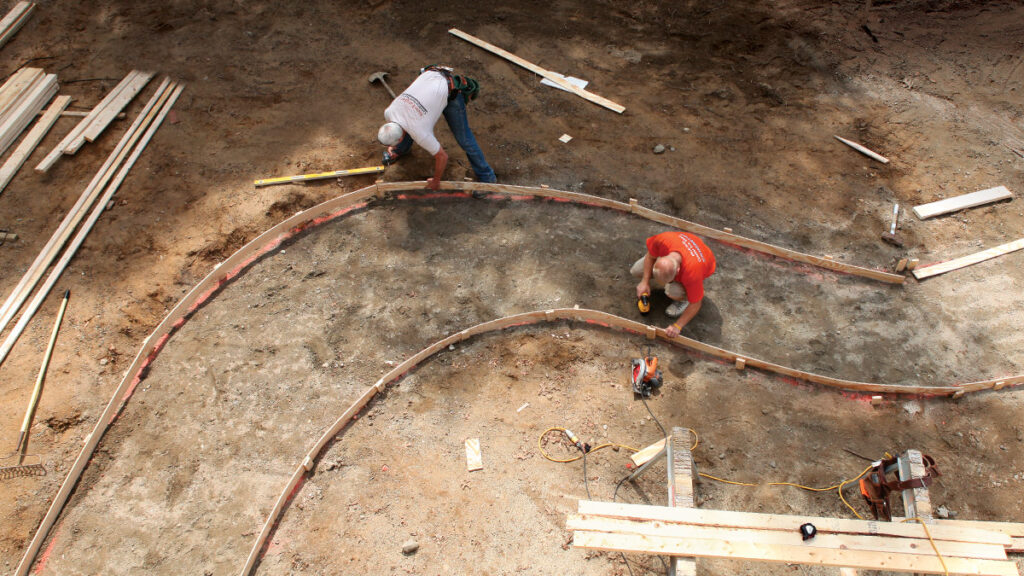
Sustainability and Plywood in Construction
The construction industry’s growing focus on sustainability has led to increased interest in plywood as an environmentally friendly alternative. Plywood is made from a renewable resource – wood – and its production involves less energy and carbon emissions compared to other construction materials. This makes it a more sustainable choice for curved concrete formwork applications.
Additionally, the reusability of plywood forms reduces waste and promotes a circular economy approach to construction. Once a project is completed, the plywood forms can be disassembled and reused for future projects, minimizing the need for new materials and reducing the overall environmental impact.
Moreover, the use of plywood in curved concrete forms can also contribute to energy efficiency in buildings. Plywood has excellent thermal insulation properties, helping to reduce heat loss and improve energy efficiency. This can lead to lower energy consumption and reduced carbon emissions, making plywood an attractive choice for sustainable construction practices.
In conclusion, plywood has become an innovative solution for constructing curved concrete forms. By understanding the basics of plywood, its application in forming curved concrete, and the advantages it brings, construction professionals can leverage its cost-effectiveness, durability, and strength. Despite the challenges it presents, such as achieving a smooth finish and preventing moisture-related issues, plywood can be effectively used for curved concrete forms with proper techniques and maintenance.
As technology advances and sustainability becomes a priority, plywood’s role in curved formwork is expected to expand, offering even greater efficiency and environmental benefits to the construction industry. With ongoing research and development, we can anticipate further improvements in plywood technology, including enhanced coatings, treatments, and manufacturing processes, that will continue to push the boundaries of what is possible in curved concrete formwork.
More read: Maximizing Efficiency with F17 Grade Plywood in Formwork